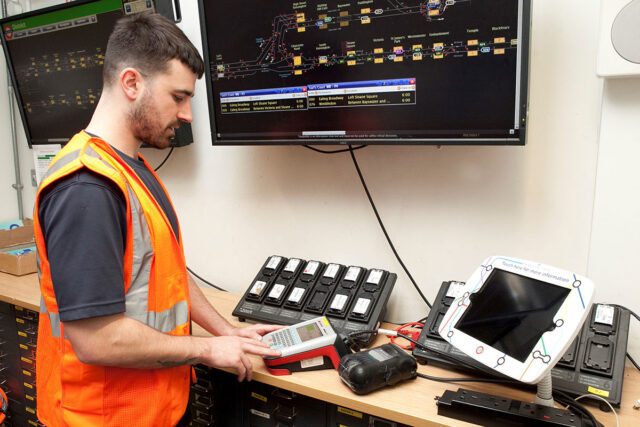
Equipment that is used for various household and industrial purposes generally requires electricity. Since electricity is a form of energy, it tends to dissipate into the surroundings. Therefore, appliances that use electricity are pretty risky if not built and used effectively. In order to protect citizens from unnecessary damage, it becomes indispensable to test regularly.
Understanding Testing Of Appliances?
PAT Testing means “Portable Appliance Testing” in abbreviation. An electronic gadget or appliance must undergo several testing stages before it can be determined if it is safe for general use. Industrial-grade appliances also require the same testing. This type of testing is carried out on a wholesomely frequent basis to ensure that all batches are regarded as safe.
How Often Are Portable Appliance Tests Done?
In order to maximize the efficiency and safety of users, Portable Appliance testing must be done regularly enough. However, it is difficult to determine whether or not the testing should be done in a particular time frame. Various factors affect how often the testing should be done to yield ideal results.
Type Of Appliance
The type of appliance affects the final decision as to how often the tests will be conducted. Ideally, appliances that are more stable can be tested in longer intervals of time. The intervals of time can range between eighteen to twenty-four months. Meanwhile, any equipment that is used by an individual in direct contact must be tested more frequently. These tests are done annually to prevent any possibility of harm directly to its users.
Portable appliances are slightly more complicated. If the appliance is being transported over long distances, the chances of slight mishandling, jerks, movements, and vibrations can contribute to significant disasters. Hence the testing of such equipment can be done between six to twelve months of regular use.
Location Of Use
Extreme weather situations would require the utilization of specific components. These devices can be installed either indoors or outdoors. Occasionally, certain parts are subjected to intense solar radiation or heat waves. Storms with severe rain and snow are also possible.
Every part of electrical equipment is adversely affected by these environmental conditions. A gadget should be able to continue operating in those conditions if it is designed to be used there. There should not be any kind of leak into the gadget. Additionally, the device should not become overheated.
Construction sites or mines are prime examples of places where there is plenty of dust and particulates. When ordinary machinery is subjected to dust over time, it will slow down and heat it up. In addition to damaging the machine parts, this boosts the warmth of the process. Anyone using it or being close to it might be at grave risk. Such outdoor devices should be tested almost every month or at the start and end of a short term project.
Sampling Results
Sampling is the process of taking samples out of a population of results. Sampling chooses a handful of results to make interpretations about the entire population. Since there is a possibility that not all equipment is tested, it is essential to sample some of them. For example, if there are two hundred drillers in a mine, not all of them can be tested at once. Therefore, some of the drillers may be tested in a cycle followed by the next set of equipment in the next cycle.
Incidental Testing
Sometimes it is essential to know whether the testing process should happen irrespective of incidents or not. If the equipment has suffered a fall or jerk in use, it should be subsequently tested. Another aspect of this random testing is that if the equipment is used more often, it will have to be tested more regularly. If an appliance does not have any incident, it can be tested at standard intervals.
Type Of Equipment Maintenance
There are various ways to maintain equipment so that the life of the appliance is long enough. There are three classical types of maintenance strategies available to a production manager. Breakdown maintenance is one of the most widely used methods which technically involves maintenance when the machine stops functioning. Only when the machine stops functioning, any effort is made to rectify it and bring it back to use. This is a low cost approach but turns out to be a reactive technique as it is not reliable.
Another great way to manage equipment is to prevent any defects from developing itself. The maintenance is done regularly to ensure that there are no breakdowns or harm to the equipment or its users. This process not only involves a more costly means of managing equipment but is also considered a standard practice in most production houses.
The third type of maintenance strategy is that of predictive maintenance strategy. It ensures that there are no such issues that develop themselves. It is similar to preventive maintenance but involves the use of specialized tools to measure exactly how the equipment is behaving and performing. It helps in understanding exactly when the breakdown may occur and the maintenance is done prior to that.
Depending upon the maintenance practices, different frequencies of portable appliance testing can be known. As and how the equipment moves through the equipment life cycle, testing differs. Portable Appliance Testing is done more often in the infant or initial stage and the decline stage when breakdown is high. In the ideal stage, where the equipment is well seasoned and yet not too old, Portable Appliance Testing is done less often.
Conclusion
Irrespective of the type of equipment, it is necessary to go for Portable Appliance Testing on the grounds that it is a regulatory requirement. The compliance with health and safety standards authorities renders it essential for all devices to undergo standard testing protocols. This ensures that there are no faults initially or over time in any appliance that is used by people, whether in households or industries.