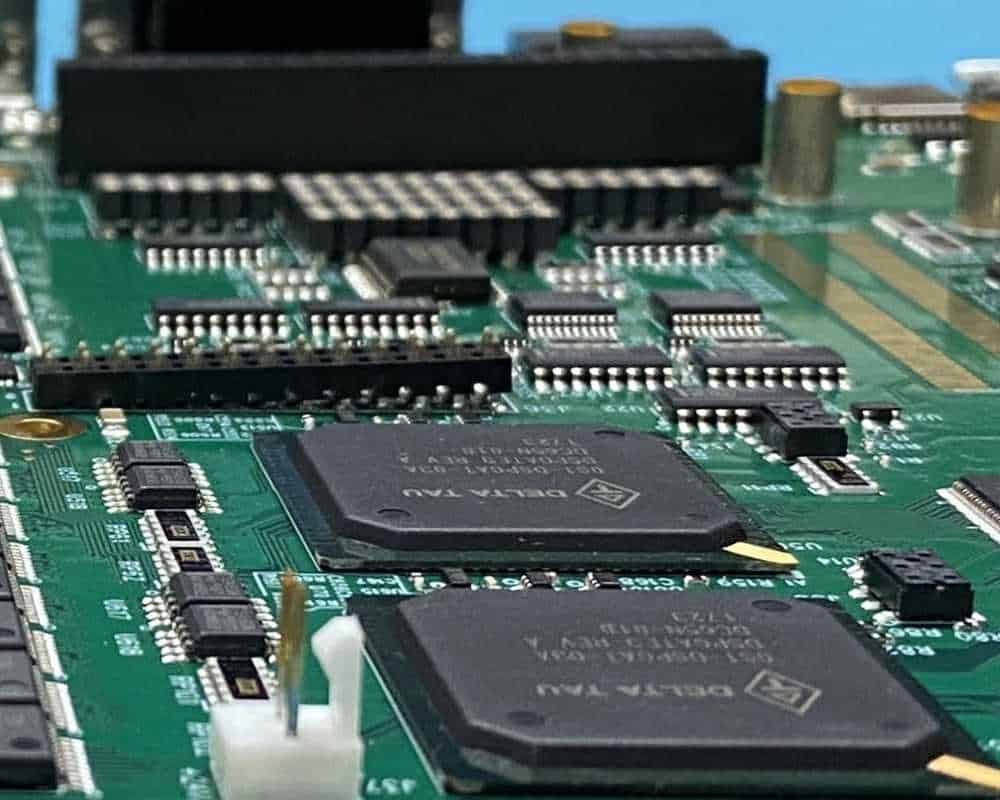
In order for your PCB to be of good quality and have a good price, you must not make mistakes at the beginning of the design. During the process, you need to constantly check the condition of the PCB, return to the previous steps and test the functions. The reason is the growing demands for printed circuit board design that you must meet if you want to succeed in business.
It is now more important than ever to make the right choices in the design phase, but also with everything else. Stick to clear design guidelines, but also the whole process when it comes to this part of the job. Keep in mind all the mistakes that can happen to you. So learn something about them so you can avoid them and finish your project.
1. Wrong design software
If you work with insufficient quality software, we are sure that you will not be able to create a quality product. That means reducing your profits, but also your reputation. Of course, finding the right software is not an easy task, but it is also not impossible. Today, you have a lot of choices, and in order to decide on the right one, you only need to notice certain characteristics. For example, you can opt for free software, but we’re not sure how many features you would have available.
That is why it is first of all necessary to take into account the needs of your business, because that is the only way you will know what you are looking for. This means that you will focus on the right options, components and more. Consider whether you need something easy to use or ready to face advanced features and complex software tasks. Before you start production, make sure that your software works well so that you do not create a large series of bad products or a series of PCBs that you will not use. That would be wasted money same as when you have problems with PCB assembly.
You can find more about it at https://vinatronic.com/blog/components-shortage-should-i-use-a-broker/
2. Poor connection between traces
Thus, incorrect trace geometry could very badly affect production. The fault is very obvious, because traces are responsible for the transmission of electrical signals between components. If their position is not precisely determined, there is a possibility of restrictions. This will affect the speed, current intensity and frequency of the signal. That is why it is important to pay attention to geometry, because it plays a huge role in this process. It is necessary to find the perfect width, but also the thickness when it comes to each trace. Less or more thickness has its advantages and disadvantages, which means that you should know how to choose the right dimensions. For example, somewhere a larger insulation trace is needed while somewhere it is not necessary.
3. Poor choice of manufacturer
This is another bad choice among others, which you can bring. Don’t let something like this ruin everything you have planned and worked on. Once you have invested a lot of time in this process, don’t skimp on it further. Take some extra time to find the right manufacturer. The job will only be well done if you dedicate yourself equally to each part of the process. For example, there are companies that have just started a business and will only ask for the cheapest price or the fastest service.
Conduct adequate research so that you do not make a mistake and decide on a manufacturer that cannot offer you good quality. This depends on several factors that influence the process of designing and manufacturing PCBs. Read reviews online, consult with friends or family if they have had cooperation with real experts. It would be good to have several choices to make a comparison. Make a list of potential companies, and write the advantages and disadvantages next to them. This approach will surely guide you on the right path, and maybe you will find the right professional that way.
4. Bad schedule
There is a growing demand for PCBs, and especially for smaller ones. This means that the layout is crucial, and many make mistakes at the very beginning of the design. The problem is a bad plan or a deviation from it. Designers today are forced to use components with smaller footprints, which means that the distance between the components is significantly reduced. If you apply a schedule that is not good enough, you automatically risk the functionality of the product.
There is a high risk of problems such as inability to connect or inconsistency. When using a large number of pins this is a particularly big problem. So do your best to ensure the functionality. This means that you will carefully determine the schedule. Such a layout should suit the needs of a particular circuit, and it is useful to always leave more space for additional components. You may need them in the near future.
5. Defects
This refers to soldering defects. Regardless of the fact that you have arranged the components correctly, you must position them in such a way as to avoid this defect. Pay attention to the number of components, because you must not place them in those places where the shorter parts will cross into the wave. This way you can create a shadow effect, which automatically affects the strength of the solder joints on the pins. If you do the right thing in this part of the job, you won’t have a problem overheating one side over the other. In such a situation, one part retreats onto that pin, and the condition is known as PCB tombstoning.
6. Lack of audit
Although this part of the job is often underestimated by people, don’t make that mistake either. Project revision is actually a very important element in the whole process. If you introduce periodic project reviews, you will meet all the high level requirements of the project. This way you will avoid design mistakes in advance.
Conclusion:
If you watch out for mistakes and work exclusively with experienced technicians, your board will meet the highest standard of the market. Keep in mind that even experienced designers can make certain mistakes, so it is important that you know equally well how to solve them. Some challenges may be unique, but there are a few common challenges we listed earlier.