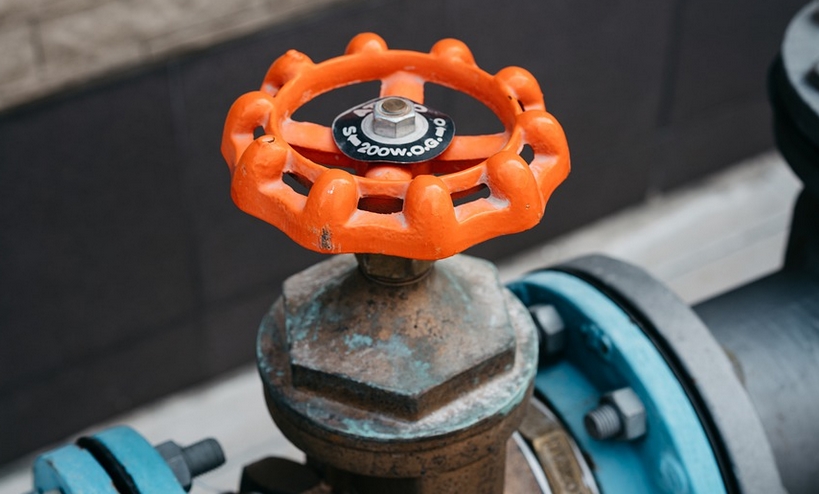
You need to construct a pipeline when setting up a plant to handle fluids like gases and oils. One thing you need to consider is your control over the substances, such as the capability to start and stop their flow. Industrial valves are necessary components of your plant that help achieve such a purpose.
Types of Industrial Valves
There are many types of these items, each with its own unique features and benefits. Before choosing the right one for your application, you first need to determine the type you need.
The three main types are displacement, ball, and check valves. Displacement regulators use a spring or other mechanical means to open and close it. Ball valves use a small ball to act as a weight that helps keep the regulator open or closed. Check valves use a set of metal balls that can be moved up and down to open and close them.
Each type of these regulator has its own advantages and disadvantages. For example, displacement ones are usually less expensive than ball or check valves and can be opened quickly using simple hand tools. However, they can also be less accurate, which can lead to leakage. Ball and check valves are usually more expensive than displacement valves but offer greater accuracy and stability.
Once you have determined which type of industrial valve is best for your application, you next need to consider the size and shape. You also need to decide whether you want a manual or automatic one. Manual regulators require someone to operate it while automatic valves require no operator input.
Finally, you need to consider the type of fluid that the valve will be used to control. Displacement valves are usually best for fluids that have low viscosity, such as water or oil. Ball and check valves are better suited for high-viscosity fluids, such as gas or oil.
Here are six tips you can try in selecting the right one for you.
1. Determine your purpose
Industrial regulators are installed alongside the pipeline to control the flow of the materials being manufactured. The word control implies various meanings, which may include starting or stopping the flow, adjusting the flow rate, changing the flow direction, and regulating pressure inside the pipes. Your intended usage will help determine the suitable valve type you need.
2. Know the correct type and size
There are many applicable types that you can use depending on your purpose. Standard configurations include globe, gate, ball valves, and more. Below is a detailed list of these industrial valve types and their basic functions.
- On/off valves — the ones that start or stop the fluid flow.
- Ball
- Butterfly
- Gate
- Rising plug
- Flow control regulators— components that help control the amount of fluid that flows per set time.
- Gate
- Globe
- Needle
- Directional flow valves — the ones that control the direction of the fluids being processed.
- Check valves
Top valve manufacturers & suppliers like XHVAL have a lot of types to offer, with varying specifications in terms of build quality and size. Consulting an expert from a manufacturer is a good step in acquiring your industrial regulator.
3. Check material compatibility
You want your components to be tough, so considering how well they can handle your materials is essential. Determining whether your chosen regulator is chemically compatible with your to-process substances matters to prevent corrosion and failure. Stainless steel ones are a popular choice with their corrosion-resistant properties.
Considering how long your regulator will last when it’s affected by corrosive substances matters in determining your repair costs and manufacturing success. Corrosion easily leads to shorter component life, and if not maintained properly, it can also be detrimental to preventing fire and explosion accidents.
4. Consider your requirements in performance
How intensive your manufacturing process will be will also be an important factor to consider. Identify whether you require high-temperature and high-pressure manufacturing needs to choose the right valve. Top choices in terms of regulator material include metals and metal alloys, including brass, stainless steel, and cast iron.
5. Factor in cleaning and repair
Controller maintenance benefits you in three facets: costs, safety, and shutdown prevention. Considering your resources in performing it is also essential to your choice. There are types designed to be maintenance-free like ball regulators, which are meant to be replaced.
Another related scenario is the placement of your chosen regulator. For example, you are using a ball valve to control the flow rate of your materials. However, this particular type is more suitable for clog resistance and on/off flow purposes. If you use the wrong type, the said part will likely experience significant wear and tear, which may lead to downtimes.
6. Weigh ownership costs
While you want to get high-quality and long-lasting industrial regulators, you also want to weigh the costs of owning them. The cost here not only refers to its cost price but also its maintenance fees. Considering the durability of the products that you purchase and their replacement or repair costs would be a good step. Maintenance checks will also require expensive downtime.
If you are planning to order industrial valves from a China-based manufacturer, shipping costs and import taxes are a few additions to your total costs. One way you can access more affordable transportation costs is by working with a top and trusted China freight forwarder.
Conclusion
Industrial valves are common but essential components of any plant. In particular, they are highly sought-after by players in the oil and gas industries. When choosing the correct industrial controller, consider your budget, performance requirements, purpose, and maintenance allowance. We are sure that you can find the one you need!